Quicktron X BULL
Quicktron provided Bull Group with an intelligent robotic system designed to achieve efficient automation throughout the entire process, from raw material delivery to finished product storage.
- First Floor Injection Molding Area: Out of 136 injection molding machines, 66 are equipped with palletizing and mobile robot material collection functions.
- Second Floor Semi-Finished Goods Warehouse and Coating Production Lines: The second floor is arranged with one semi-finished goods warehouse, six coating production lines, and one finished goods warehouse. Semi-finished goods are transported upstairs via material tote elevators, where conveyor sorting lines and mobile robots ensure precise storage. Coated finished products are transported by mobile robots to the entrance of the finished goods warehouse and manually palletized for storage.
Challenges And Objectives


Customers Pain Points:
The customer urgently needs to improve efficiency and automation levels while reducing labor costs in the logistics operations between the injection molding and coating workshops. The material flow and management between the injection molding and coating workshops face numerous challenges and require an efficient logistics solution.
Quicktron carefully designed a corresponding logistics plan based on the logistics needs and specific metrics of each production stage. From injection-molded white parts to coated finished products, and from jig storage to white part warehouses, each stage has clear logistics routes and operational procedures.
Solution and Benefits
In this warehouse space totaling 2,400 square meters, a variety of robots have been deployed, including Moving Robots with dual conveyors, Moving Robots (M100B, industrial version), telescopic robots (C41B, standard version with gripper), and Moving Robots (M5A), totaling 27 units.
- Efficiency Improvement:The automated logistics system achieves a handling capacity of up to 160 totes per hour, with a daily throughput of 5,000 totes of injection-molded white parts and 4,750 totes of coated finished products.
- Process Optimization:Automation and intelligence have reduced human errors, while real-time inventory management has optimized material scheduling and inventory control.
Robot Type and Quantity | ➡️ Dual-Layer Roller Moving Robots: 10 units; M100 Moving Robots: 10 units; C41B Single Depth (Gripper) Robots: 2 unit; M5A Moving Robots: 5 units |
Full-Pallet Storage Area | ➡️ Goods are stored in a semi-finished goods warehouse for full pallets of semi-finished products. |
Tote Storage Area | ➡️ The second-floor semi-finished goods warehouse stores loose items. |
Storage Objects | ➡️ General turnover totes, jig turnover totes, plastic pallets |
Storage Type | ➡️ Mobile robots transport goods to designated storage areas, managed with manual kitting preparation at shipment points. |
Inbound/ Outbound Type | ➡️ Mobile robots, elevators, and conveyor lines work together for automated inbound and outbound processes. |
Storage Volume | ➡️ Effective storage capacity: 10,000 totes (expandable to 24,000 totes) |
Daily Outbound Volume | ➡️ Injection-molded white parts: approximately 5,000 totes/day; Coated finished products: approximately 4,750 totes/day. |
Application Scenarios:
- Injection Molding Workshop: Mobile robots, guided by the MES system, handle full and empty totes, delivering them to and from the conveyor line.
- Semi-Finished Goods Inbound/Outbound Process:
Category A | ➡️ Inbound: Goods are automatically transported, palletized, and stored by robots; Outbound: Robots transport goods to the production line, with manual picking and pallet replenishment guided by PDA. |
Category A Categories B & C | ➡️ Inbound: Robots transport goods after WMS identification; Outbound: Orders trigger robot transport to the outbound station for manual pallet placement. |
- Finished Goods Handling: Inbound: WMS directs robots to store scanned products; Empty Pallet Handling: PDA triggers robot transport tasks.
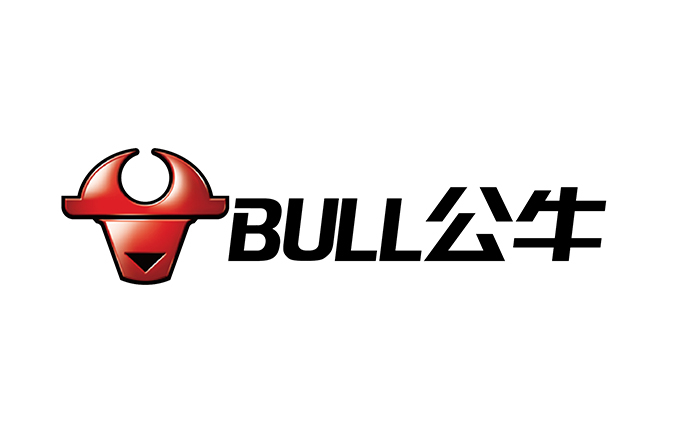
"Quicktron’s cutting-edge robotics solution has transformed our logistics and production processes at Bull Group. The substantial increase in efficiency, remarkable error reduction, and significant cost savings have had a tremendous impact on our operations. We are now able to deliver products more efficiently from raw material delivery to finished product storage, all while optimizing workflow and reducing labor costs."
BULL GROUP
Related Cases
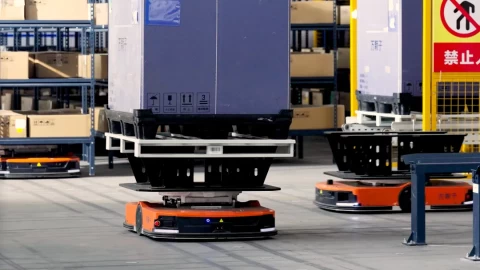
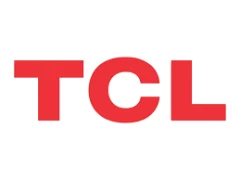
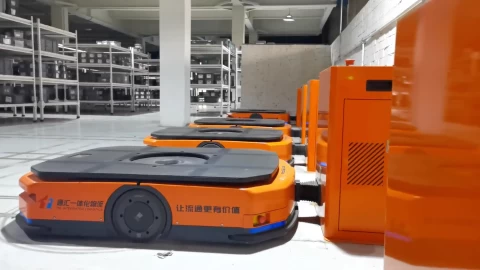
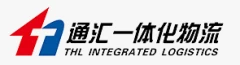
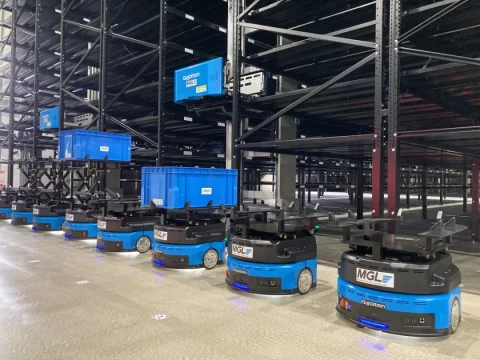
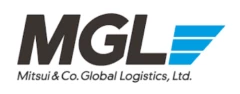
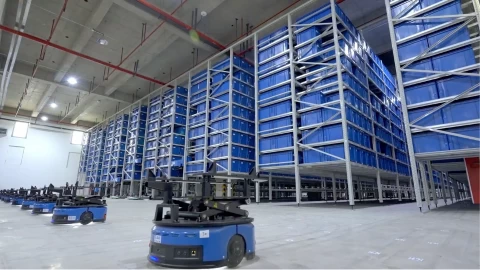
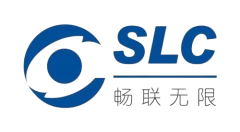
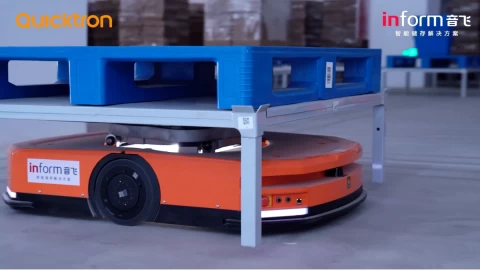
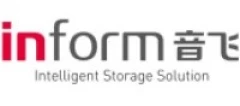
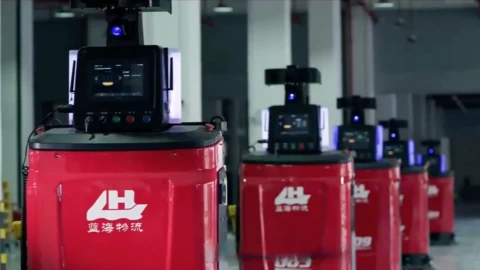
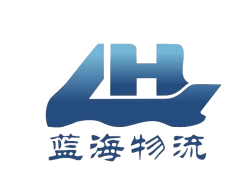