Quicktron X Radial
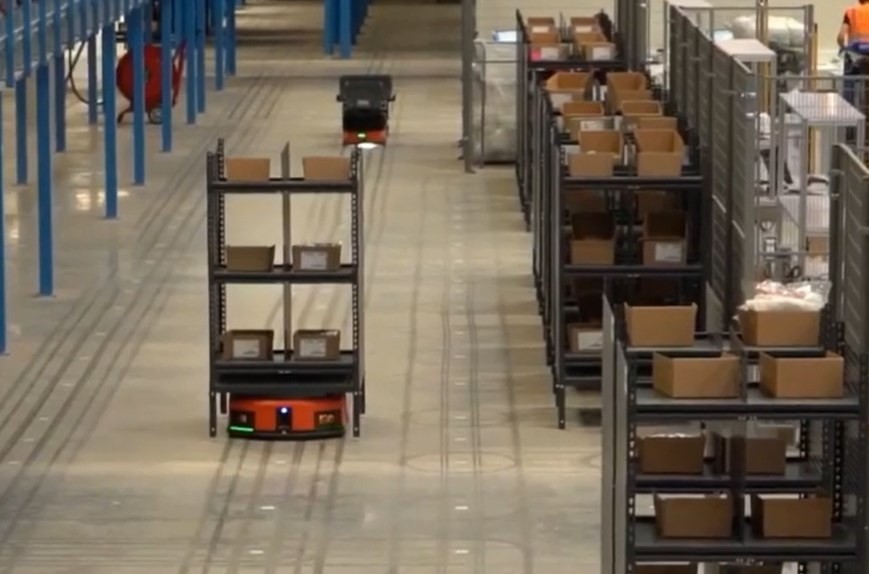
Radial Inc., a leader in e-commerce fulfillment and tech solutions for premier brands, prioritizes delivering high-value customer experiences, flexibility, scalability, and business focus. However, as e-commerce orders continued to escalate, the company faced the challenge of adapting to agile automation. They sought streamlined resource allocation and aimed to consolidate the storage of diverse items under one roof for centralized processing.
Challenges And Objectives
Escalating E-commerce Orders: The rapid growth in e-commerce orders necessitated a more agile and automated approach to fulfillment.
Resource Allocation Inefficiencies: Inefficient resource allocation was impacting productivity and operational efficiency.
Prolonged Lead Times: Prolonged lead times needed to be minimized to meet customer expectations.
Storage of multi-sized goods: The need to consolidate the storage of goods of all sizes under one roof for centralized processing presented a complex challenge.
The primary objective was to:
Implement a streamlined and centralized fulfillment system capable of handling items of all sizes efficiently.
Solution and Benefits
The facility features over 299 mobile robots and a next-gen hybrid goods-to-person (G2P) automation system. Apart from the large scale, the site has 2 key features. First, the ability to handle totes, pallets, and shelves, all at once through centralized workstations, and second, the automated replenishments of the put-away walls to fast-track fulfillment operations. The new facility significantly accelerates Radial's business operations, allowing it to process millions of items per year. Dual picking points were introduced to minimize operator idle time, and inbound and returns stations were combined to optimize tote utilization.
Seamless software integration: By integrating RCS, WCS, and WES software with Radial's WMS, alongside equipped workbenches and safety measures Quicktron manages the efficient movement of 299 robots in a vast 8500 sqm area, effectively addressing flow and storage needs.
Efficiency Soars: The system achieved an impressive daily output efficiency of 40,000 order lines.
Hybrid Workstations: The introduction of hybrid workstations made the processing of multi-shaped goods.
Dual Picking Points: Dual picking points minimized operator idle time, improving overall efficiency.
Optimized Tote Utilization: Combined inbound and returns stations optimized tote utilization.
Labor Cost Savings: Labor costs were reduced by a substantial 40%.
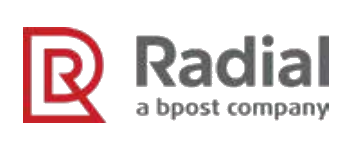
“This not only caters to our immediate warehousing needs but also paves the way for future expansions to better serve our valued customer for years to come. We are very proud to work with Quicktron on this new site which is setting new standards in the industry."
Hans Vansweevelt, COO at Radial
Related Cases
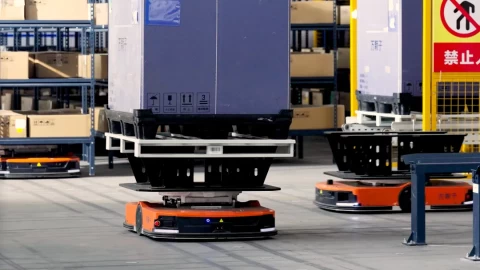
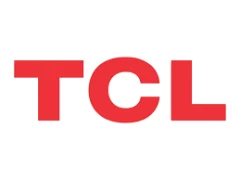
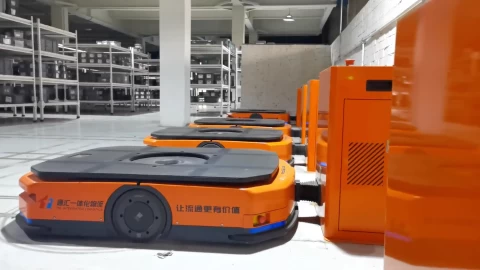
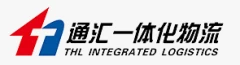
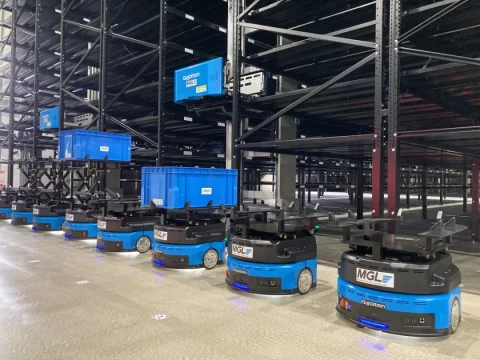
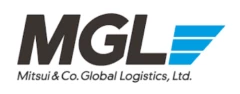
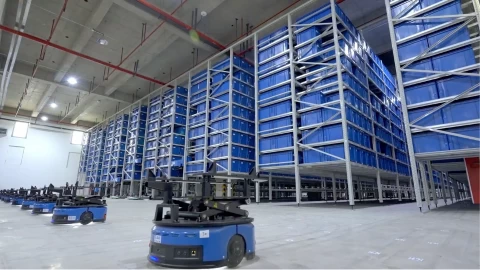
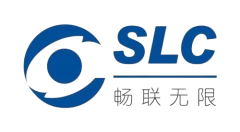
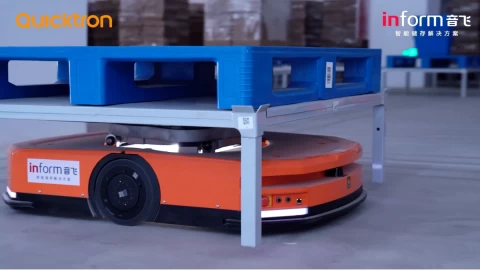
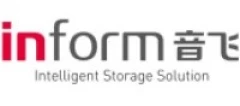
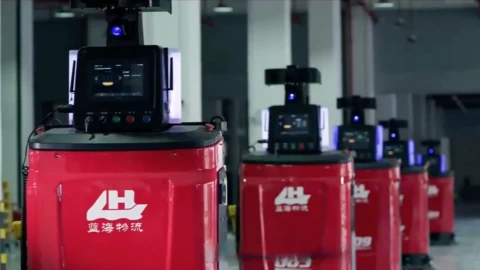
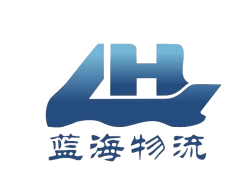