Quicktron X Maersk
A.P. Moller-Maersk, a leading integrated logistics company offering distribution and fulfillment solutions in retail, wholesale, and e-commerce, faced formidable challenges in the realm of omnichannel fulfillment services. These challenges included escalating labor costs and unpredictable surges in seasonal orders. In response, Maersk sought to enhance picking efficiency for both B2B and B2C orders to navigate this critical juncture.
Challenges And Objectives
Omnichannel Fulfillment Complexity: The company needed to streamline its operations to effectively handle the complexities of omnichannel fulfillment services, which required a seamless flow of goods to meet diverse customer demands.
Labor Cost Escalation: Escalating labor costs posed a significant operational challenge. Reducing reliance on manual labor and optimizing efficiency became imperative.
Seasonal Order Spikes: Unpredictable spikes in seasonal orders strained Maersk's capacity to meet demand efficiently. It was crucial to find a solution that could adapt to these fluctuations in workload.
Storage utilization: Effective storage utilization to increase the capacity while reducing cost was also one of the targets.
The primary objectives were to:
Enhance picking efficiency for both B2B and B2C orders.
Mitigate disruptions to daily operations caused by the challenges.
Achieve greater efficiency with a lean workforce.
Solution and Benefits
Maersk adopted Quicktron's QuickBin solution, which featured 84 mobile robots (C56+ M5). This innovative approach delivered remarkable results:
Disruption Mitigation: Quicktron's QuickBin solution proved indispensable in mitigating disruptions to daily operations, allowing Maersk to maintain smooth logistics processes even during peak periods.
Efficiency Enhancement: Through the synergy of advanced software and hardware, a lean team of just 6 workers achieved three times greater efficiency in handling order spikes. Picking efficiency soared to 300%.
Inventory Management: Maersk was able to effectively manage an impressive 3000 SKUs with a remarkable four-fold increase in picking efficiency. This allowed for the efficient handling of a vast inventory of 400,000 items.
Expanded Capacity: The automated area expanded to 1200 square meters, accommodating 84 autonomous mobile robots (AMRs) and 6 workstations. This expansion resulted in a 60% increase in storage capacity.
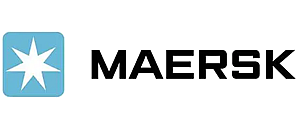
“QuickBin solution has transformed the way we do business, allowing us to navigate the complex terrain of logistics with unparalleled efficiency and adaptability.”
Maersk
Related Cases
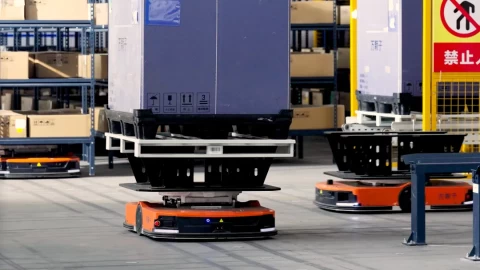
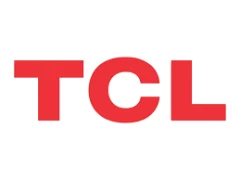
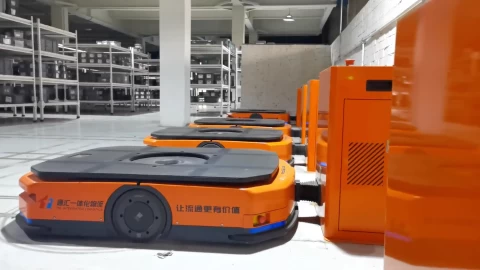
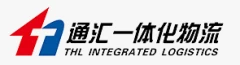
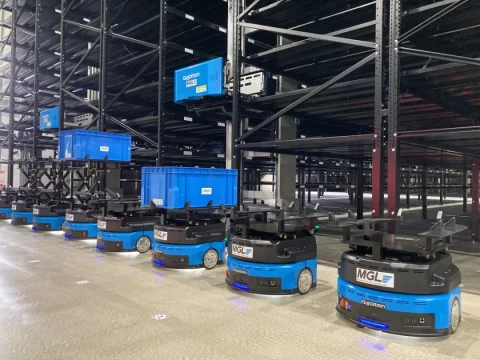
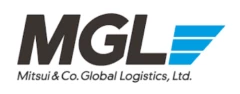
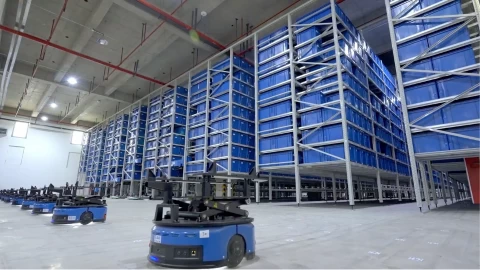
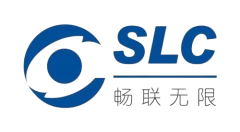
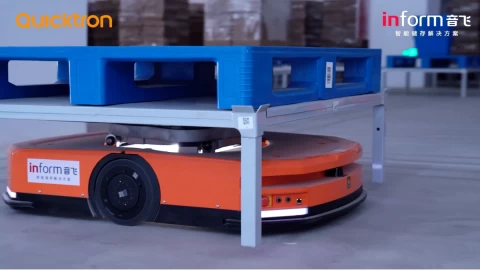
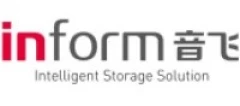
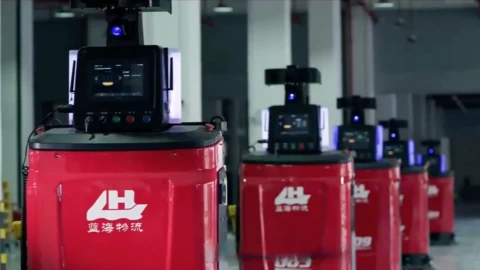
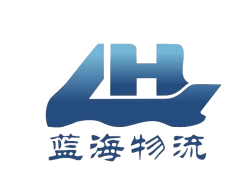