Changing Consumer Behavior is Driving Robots in Warehouses
In this article, we will explore how consumer behavior has been a driving force behind the need for robots in warehouses...
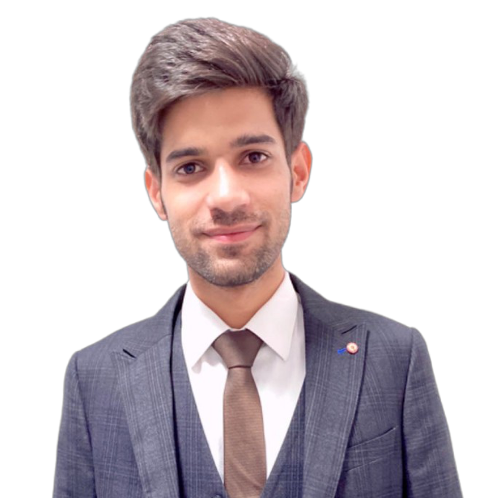
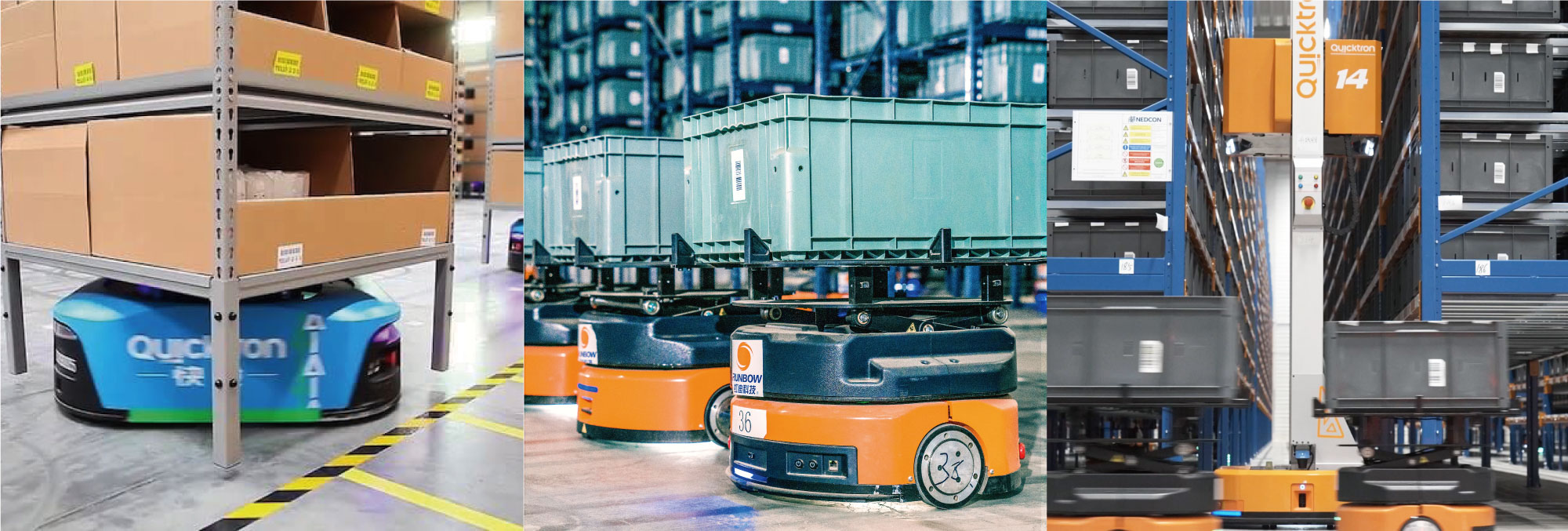
The COVID-19 pandemic has had a major impact on consumer behavior. We have seen a dramatic shift toward online shopping in the past few years. Insider Intelligence’s statistics revealed that e-commerce sales are projected to exceed $6.3 trillion in 2023. This shift in consumer behavior is putting immense pressure on warehouse operations and distribution centers to adapt and optimize their processes to meet the demands for faster shipping times.
One way that warehouses are responding to this challenge is by adopting robots in warehouses which has been increasing at an unprecedented rate in recent years. Robots can help to improve efficiency, accuracy, and productivity in warehouses. They can also help to reduce the risk of injuries to workers. This shift in behavior also elevated the role of the warehouse in the customer relationship, making it critical to meet the expectations of customers who want their purchases delivered quickly and accurately. As a result, warehouse automation is becoming a vital part of the retail ecosystem, requiring significant changes to keep up with the pace of change.
In this article, we will explore how consumer behavior has been a driving force behind the need for robots in warehouses.
Change in consumer behavior!
The accelerating shift towards online shopping, with e-commerce growing two to five times faster than before the arrival of COVID-19, as reported by McKinsey. Customers now demand more personalized online shopping experiences. A staggering 70.6% of shoppers surveyed by Unfolded via Internet Retailing have preferred shopping online rather than in-store, even after the COVID restrictions. For retailers to thrive in a post-pandemic landscape, a sound e-commerce business strategy is essential. The rise of e-commerce in the post-pandemic world has sparked the robolution in fulfillment centers.
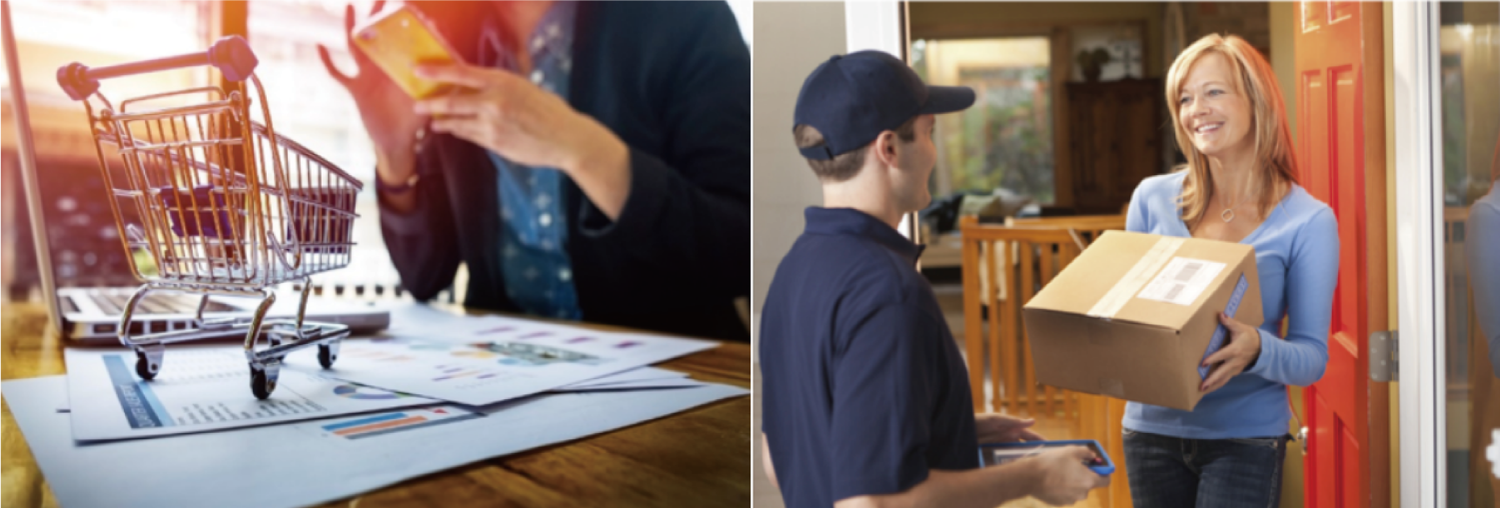
Changing consumer expectations is also driven by the need for seamless omnichannel commerce and speedy fulfillment, the supply chains of manufacturers, retailers, distributors, and 3PLs have become increasingly complex. In the midst of these changes, warehouses have faced the biggest challenges, managing rising demand and tighter shipping deadlines amidst a changing business landscape.
The use of robotics and automation as offered by Quicktron can assist companies in managing the effects of rising complexity in their warehouses. Nonetheless, identifying the appropriate starting point for your organization's specific requirements and determining how to attain optimal levels of automation is imperative for achieving success.
Robots can make fulfillment operations more efficient!
By using Quicktron's mobile robots (AMR/AGV) in warehouses, can streamline their operations and reduce the time it takes to fulfill orders. These robots can work around the clock, allowing companies to process orders much more quickly than they would be able to with human workers alone. By using robots in the warehouse, companies can reduce the likelihood of errors and ensure that orders are fulfilled accurately and quickly. This, in turn, can lead to higher customer satisfaction and increased loyalty. For example, companies such as Quicktron are now using mobile robots that can autonomously move around the warehouse to pick, sort, and transport goods. These robots are particularly useful in large warehouses where it may be difficult for human workers to navigate quickly and efficiently. Additionally, using robots with machine-learning capabilities helps them identify and sort items more quickly and accurately.
Increased efficiency: Mobile robots can automate tasks currently performed by humans, leading to increased efficiency and productivity. With Quicktron’s G2P solution warehouse businesses can boost efficiency by 300%
Improved safety: Our Mobile robots can help to improve safety by performing tasks that are dangerous or difficult for humans to do.
Reduced costs: Mobile robots can help to reduce costs by eliminating the need for human labor.
Improved quality: Mobile robots can help to improve quality by performing tasks more consistently and accurately than humans with a 99.99% accuracy rate.
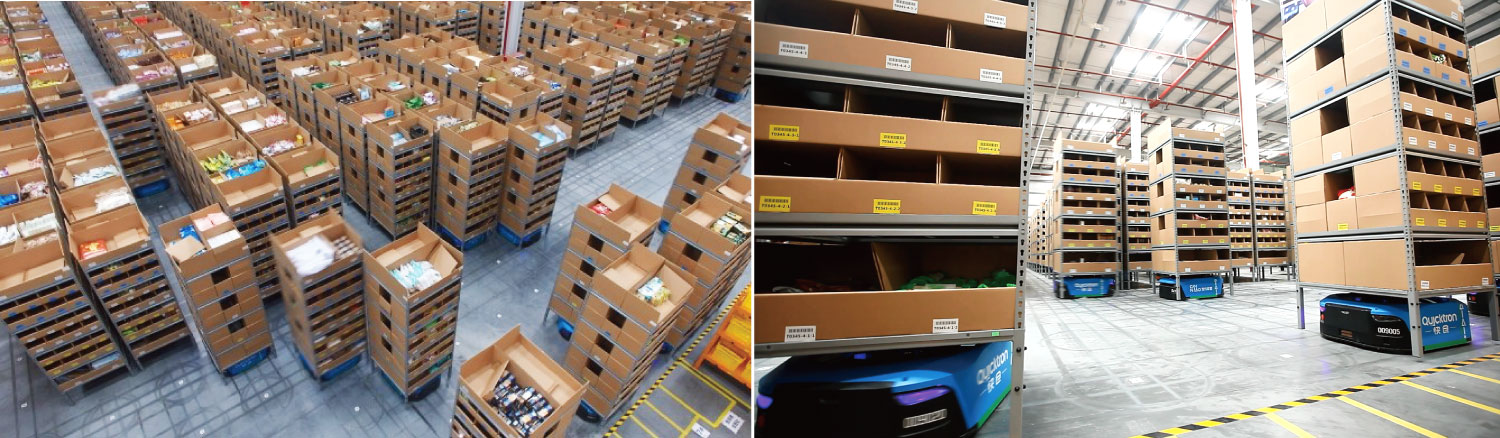
In addition to driving the need for robots in the warehouse, consumer behavior is also influencing the design of these robots. For example, companies are now developing robots that are human-friendlier in appearance and movement. This is because consumers are more likely to trust and feel comfortable with robots that are safer and more productive. Additionally, companies are designing robots with features like voice recognition and touchscreens to make them more user-friendly for human workers.
Overall, it is clear that consumer behavior is a driving force behind the increasing use of robots in warehouses. As consumers continue to demand faster, more efficient, and more accurate delivery times, companies will be under pressure to invest in automation technologies like robots. This trend is likely to continue in the coming years, as technology continues to advance and consumer expectations continue to evolve. At Quicktron Robotics, we understand that the success of our clients' businesses depends on their ability to deliver high-quality products quickly and efficiently. By providing innovative robotic solutions such as QuickBin and Shelf based Goods-to-person picking systems that can help them meet the demands of their customers, we are proud to play a role in driving the adoption of robotics and automation in the warehouse.
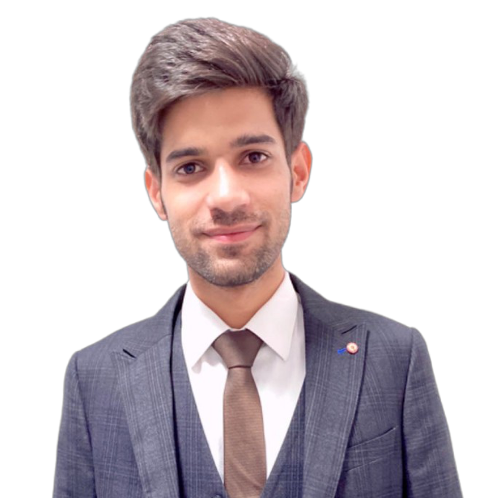
Arslan crafts compelling content, executes social media campaigns, and masters online ads, webinars, podcasts, and copywriting. He builds strong relationships with clients, empowering them with support and resources to achieve their sales goals. Leveraging data insights, he refines strategies and collaborates seamlessly to stay ahead of the digital curve.